Baptist Mills & the trouble with brass
- GVHeritage Groups
- Aug 9, 2017
- 5 min read
In 1710 the foundry at Cheese Lane, which is where the lead shot tower still stands today, was valued at £1,738!

Brass is made by combining Copper and Zinc at high temperatures and since the 16th century people had been attempting (unsuccessfully) to produce brass in Britain. For a long time all brassware was imported into Britain from Austria, Germany, France and the Low Countries where brass industries had been flourishing since the 14th century. Brass goods were produced in England by craftsmen using imported raw brass, called latten, or finished goods themselves were imported. London based merchants had been given a Royal Monopoly on importing and re-exporting this continental latten and finished brassware and so they had a strong incentive to block attempts to manufacture brass in Britain. The Mines Royal Company and the Mineral and Battery Works Company were the two mining monopoly companies incorporated by royal charter in 1568.
After the English Revolution the merchants began to enjoy a less influential position with the political classes and in 1689 the Royal monopoly on brass making ended and at Baptist Mills the Bristol Brass Company was formed by Quaker merchants (including Nehemiah Champion II from Stapleton) in 1702 on the site of an old grist mill on the River Frome.
Baptist Mills Brass Works
The site for the Baptist Mills Brass Works was chosen primarily as it sat next to the River Frome which powered the works. Both charcoal and coal were available locally and the City and Port of Bristol were close by. Additionally a copper works had been established in 1698 in Conham on the River Avon and zinc was available from Clifton Downs and the Mendip Hills.
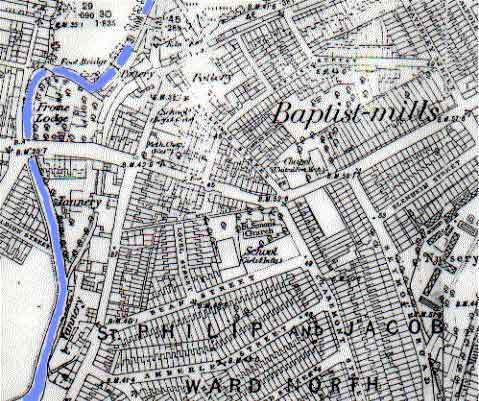
Expansion into Cheese Lane
Abraham Darby (1678-1717) was the manager of the Baptist Mills Brass Works and in 1703 he started a pot foundry in Cheese Lane to cast pot-bellied iron pots in sand, but he failed. Instead in 1704 he went to Holland to spy on the industrial techniques of coal fired furnaces and the production of large brass pots. Here he recruited a number of skilled Catholic workers and brought them back to Bristol (some with their families) to work at Baptist Mills. In 1707 Darby, alongside his backer Thomas Gouldney and with the invaluable assistance of the Welsh-born Quaker John Thomas, set up an iron foundry using pig iron from the Forest of Dean and made the first use of a reverberatory furnace in the iron industry making coal a fuel which could be used by the iron founders. This paved the way for the mass production of affordable cast iron hollowware (which were lighter, about a third of the weight of previous iron pots) and the establishment of the British iron trade. It also allowed for the production of more complex shapes and was an important factor in the development of parts of future steam engines and engineering products.
So commercially important was this discovery that it was carried out in the utmost secrecy – even the keyholes of the building were stopped up to prevent others from spying on their work! It is recorded that other industrialists tried to poach John Thomas and offered to double his wages if he left Darby’s employment. An article of Agreement lasting three years was drawn up between Darby and Thomas which increased Thomas’ wages and guaranteed his board and lodgings providing that he did not divulge ‘to any other person on or about casting Iron Potts nor will disclose the method to anyone’.
In 1710 the foundry at Cheese Lane, which is where the lead shot tower still stands today, was valued at £1,738!
Bristol Brass and Wire Company
In 1709 the Bristol Brass Company merged with the Brass Wire Works of Esher, Surrey to form the Bristol Brass and Wire Company (the joint company was valued at £16,000). The original partners who put in the necessary capital to the Bristol Brass Company included Nehemiah Champion II, whose son Nehemiah Champion III became more and more responsible for the running of the Company in 1709, when Abraham Darby left as manager.

Copper
In around 1710 the Company built its own Copper Works known as ‘the Cupolas’ on land by the River Avon by Crew's Hole and Trooper’s Hill under the control of John Coster and his son Thomas Coster. This added to the Copper supply from Abraham Elton's smelting works at Conham. The Copper Works became the main industry in the vicinity of Troopers Hill. Copper ore was brought by boat, mainly from Cornwall and north Devon and coal was sourced locally and most of the copper that was produced was used in the Company’s manufacturing at Baptist Mills.
By 1712, it is estimated that the Company produced between 400-533 tons of brass per year. Its 25 furnaces at Baptist Mills alone, which used 200 tons of copper a year, are estimated to have produced some 250-260 tons of brass a year. By the early 1720s there were 36 furnaces for making brass at Baptist Mills and the Company’s copper works were the ‘most considerable’ in England according to a Swedish mine official Henric Kahlmeter (Sweden was worried about the metallurgical advances being made in Britain as it was threatening their export trade). Ten years later Swedish scientist Emanuel Swedenborg described Baptist Mills as ‘the principal place where English brass is made’ at a time when 300 tons of brass was being produced each year from 6 Brasshouswes.
In 1725 the Troopers Hill Copper works employed 33 men hwo were paid 6/- a week and it was producing some 150 tons of copper a year. In 1734 the Company took over a copper company in Redbrook on the Wye becoming The United Brass Battery, Wire and Copper Company of Bristol, Esher, Upper Redbrook and Barton Regis.
Such was the continuing technological advance in brass manufacture in Bristol that by 1740 there was no need to fear competition from abroad and Thomas Coster was elected Bristol’s MP in 1734, further strengthening Bristol’s brass and copper manufacturing interest in London. Some would claim for this reason Bristol is the birthplace of the Industrial Revolution.

Zinc and the Champion connection
Nehemiah Champion III had three sons, John (1705-1794), another Nehemiah IV (1709-1782) and the youngest William (1710-1789). William travelled extensively to the continent to learn the art of brass making, returning to Bristol in 1730. He then experimented at Baptist Mills and Hanham with producing metallic zinc sulphide (which at that time was imported from India and Asia at a high price) from English calamine. He was the first man in the country to produce zinc on a commercial scale and it took him about six years to achieve success. He obtained a patent for his method in July 1738 and his system remained in production for over 100 years.
This was an important development for the Company as zinc prices were rising extremely fast. However it was also a double edged sword as there was an over-importing of zinc at this time to take advantage of the high price and so prices fell, leaving Champion with 200 tons of his high quality zinc which lost him £4,000!
and the inevitable demise
The Company established a brass warehouse in central Bristol near St Philip’s Church backing onto the old Queen Street giving it access to shipping and barge traffic. By the 1760s the Stock value of the Company was put at £200,000 with an annual profit of £8,000 but the relative importance of Baptist Mills works had declined by the 1730s as the Company started to favour it’s works in Keynsham and Warmley and by the 1830s Bristol’s brass industry was overtaken by competition from the Midlands (although the last mill in Keynsham didn’t close until 1928).
Baptist Mills today...


